Air compressor gauges play a crucial role in ensuring the efficient and safe operation of air compressors. These gauges provide valuable information about the pressure levels within the compressor tank and the output pressure being delivered to various tools and equipment. By monitoring these pressure readings, users can maintain optimal performance, prevent equipment damage, and ensure the safety of both operators and the surrounding environment. Air compressor gauges allow for precise adjustments of pressure settings, enabling users to match the requirements of specific tools and applications. Additionally, they serve as essential diagnostic tools, indicating any potential leaks, blockages, or malfunctions within the compressor system. With accurate and reliable gauges, operators can make informed decisions, optimize productivity, and maintain the longevity of their air compressors.
What is an Air Compressor Gauge?
An air compressor gauge is a measuring instrument specifically designed to monitor and display the pressure levels within an air compressor system. It serves as a visual indicator, typically featuring a dial or digital display, that shows the current pressure reading in pounds per square inch (PSI) or other applicable units of measurement. The primary purpose of an air compressor gauge is to provide users with accurate and real-time information about the pressure conditions within the compressor tank and the output pressure being delivered to connected tools and equipment. This information is crucial for maintaining optimal performance, preventing equipment damage, and ensuring safe operation. By monitoring the gauge, operators can adjust pressure settings, detect abnormalities or deviations, and take appropriate action to troubleshoot and maintain the efficiency of the air compressor system.
A typical air compressor gauge consists of several key components designed to accurately measure and display pressure levels. The gauge is housed in a durable casing, often made of metal or plastic, to protect its internal mechanisms. At the heart of the gauge is a pressure sensing element, commonly a Bourdon tube or diaphragm, which reacts to changes in pressure by moving or deforming. This motion is then transmitted to a mechanical linkage or a digital sensor, which converts it into a readable pressure value. The gauge usually features a dial or digital display with clear markings denoting the pressure units, such as PSI or bar. A needle or numerical display provides the actual pressure reading. You’ll find that most air compressor gauges incorporate a pointer stop or a peak hold mechanism to retain the highest pressure reached. The gauge may also include a calibration screw or knob for adjusting the accuracy of the readings. Overall, the design of an air compressor gauge ensures durability, accuracy, and ease of reading, enabling operators to monitor pressure levels effectively and make informed decisions based on the displayed information.
Are there Different Types of Air Compressor Gauges?
There are several different types of air compressor gauges available, each with its own unique features and applications. One common type is the analog gauge, which uses a mechanical system to display pressure readings on a dial. Analog gauges are straightforward to read and offer a wide range of pressure measurement options. Another type is the digital gauge, which utilizes electronic sensors to provide precise and accurate pressure readings in a digital format. These gauges often offer additional features like backlighting and the ability to switch between different units of measurement. Furthermore, there are combination gauges that combine analog and digital displays, allowing users to choose their preferred method of reading the pressure. Specialty gauges, such as differential gauges, are designed to measure the difference in pressure between two points within the air compressor system. These gauges are commonly used for diagnostic purposes and troubleshooting. Additionally, some gauges come with integrated pressure switches, which allow for automatic control of the compressor’s on/off cycles based on preset pressure thresholds. The availability of different types of air compressor gauges ensures that you can select the most suitable one for your specific needs and preferences.
How does an Air Compressor Gauge Work?
The functioning of an air compressor gauge is relatively straightforward. The gauge is connected to the air compressor system through a pressure line or port, allowing it to measure the pressure inside the system. When the compressor operates, it generates compressed air, which builds up pressure in the tank or reservoir. This pressure is transmitted to the gauge through the connection, causing the gauge’s sensing element, such as a Bourdon tube or diaphragm, to deform or move in response to the applied force. As the sensing element moves, it activates a mechanical linkage or digital sensor that translates the motion into a readable pressure value. The resulting pressure reading is then displayed on the gauge’s dial or digital screen, allowing users to monitor the pressure levels in real-time. By observing the gauge, operators can adjust the compressor’s settings, detect any abnormal pressure conditions, and take appropriate action to maintain safe and efficient operation. An air compressor gauge functions by converting the applied pressure force into a visual representation that enables users to monitor and control the pressure within the system.
Understanding Pressure Measurement and Units Used in Air Compressor Gauges
Pressure measurement is an essential aspect of air compressor gauges as it provides crucial information about the force exerted by compressed air. Pressure is defined as the amount of force applied to a given area, and it is commonly measured in pounds per square inch (PSI) or bar. In an air compressor gauge, the pressure measurement is typically indicated by a needle on an analog dial or displayed numerically on a digital screen. The gauge’s sensing element, such as a Bourdon tube or diaphragm, reacts to the applied pressure and translates it into a readable value. The PSI unit is commonly used in air compressor gauges, especially in North America. It represents the force exerted by one pound of pressure per square inch of area. The scale on the gauge dial is marked with increasing PSI values, allowing users to observe and adjust the pressure levels accurately. Another widely used unit of pressure is bar, commonly used in Europe and many other parts of the world. One bar is equivalent to approximately 14.5 PSI. Air compressor gauges that use the bar unit will have the corresponding scale displayed on the gauge dial or digital screen. Additionally, there are other units of pressure used in specific industries or applications. For instance, kilopascal (kPa) and megapascal (MPa) are commonly used in scientific and engineering contexts. These units offer a more precise measurement of pressure, with 1 MPa equivalent to 1,000,000 pascals or approximately 145 PSI. It is important for users of air compressor gauges to understand the units being used and ensure that they match the requirements of their specific tools and applications. Properly monitoring and adjusting the pressure levels within the compressor system is vital for efficient operation, equipment safety, and optimal performance.
What is the Gauge’s Role in Air Compressor Systems?
Air compressor gauges play a vital role in ensuring the efficient and optimal performance of air compressors. They enable users to regulate and adjust the pressure levels within the compressor system, ensuring that the desired pressure is maintained for optimal operation. By matching the pressure output to the specific requirements of tools and equipment, operators can achieve efficient performance and prevent potential damage. Additionally, air compressor gauges serve as diagnostic tools by detecting pressure loss or fluctuations, indicating potential leaks in the system. Monitoring the pressure readings on the gauge helps identify issues such as clogged filters or worn-out valves, allowing for timely maintenance and repairs to maintain efficiency. Furthermore, gauges prevent overloading by providing clear indications of pressure levels, preventing excessive strain on the motor and ensuring optimal performance. Overall, air compressor gauges facilitate precise pressure control, prevent system issues, and contribute to the overall efficiency and longevity of air compressors.
Recommended Pressure Ranges for Air Compressor Gauges
Recommended pressure ranges can vary depending on the specific application and the tools or equipment being used, so it’s important to consider the recommended PSI specific to each use case. In industrial applications and settings, pneumatic tools like impact wrenches generally operate well within a range of 90-120 PSI (6.2-8.3 bar). For automotive applications, standard tire inflation typically requires gauge pressures ranging from 30-35 PSI (2.1-2.4 bar), but it is important to refer to specific tire pressure recommendations. Paint sprayers usually operate effectively between 30-50 PSI (2.1-3.4 bar), while airbrushing for artistic purposes typically requires lower pressures in the range of 15-25 PSI (1-1.7 bar). Each air tool, such as nail guns or pneumatic drills, may have its own specific pressure range, so referring to the manufacturer’s instructions or specifications is crucial. These recommended pressure ranges serve as guidelines to ensure safe and optimal performance based on industry standards and specific tool requirements.
How to Maintain your Air Compressor Gauge
Maintaining and cleaning an air compressor gauge is essential to helping extend the life of your air compressor gauge and ensure its accuracy and reliability in monitoring pressure levels. In doing so, here are some tips to keep in mind:
Regular Inspections: Perform routine visual inspections of the gauge to check for any signs of damage, such as cracks, dents, or loose parts. Address any issues promptly by replacing or repairing damaged components.
Cleanliness: Keep the gauge and its surrounding area clean. Regularly wipe the gauge with a soft, lint-free cloth to remove dust, dirt, and any other debris that may accumulate on the dial or digital display. Avoid using harsh chemicals or abrasive cleaners that can damage the gauge’s surface.
Avoid Moisture and Condensation: Moisture can affect the accuracy of the gauge and lead to corrosion. Take measures to prevent moisture buildup by ensuring proper ventilation in the compressor area, addressing any leaks in the system promptly, and using moisture traps or separators in the air compressor setup.
Avoid Excessive Vibration: Excessive vibrations can impact the gauge’s accuracy and durability. Securely mount the gauge to minimize vibrations and use rubber or foam padding as necessary to dampen any vibrations from the compressor or surrounding equipment.
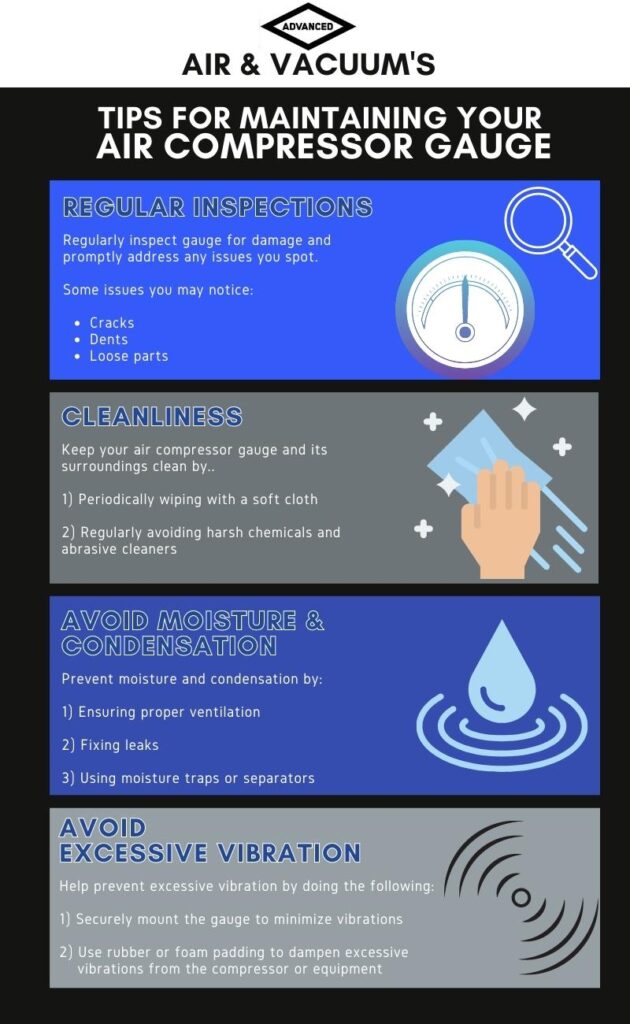
Common Issues with Air Compressor Gauges
While air compressor gauges are generally reliable, they can experience a few common problems. Here are some typical issues and their potential solutions:
1. Inaccurate Readings: One common problem is inaccurate pressure readings on the gauge. This could be due to gauge calibration issues or damage to the internal components. To address this, first, ensure that the gauge is properly calibrated by following the manufacturer’s instructions. If recalibration doesn’t resolve the issue, consider replacing the gauge with a new one.
2. Gauge Damage: Gauges can be subject to damage from impacts, vibrations, or environmental factors. Cracked or broken dials, damaged glass, or loose components can compromise the accuracy and functionality of the gauge. If the damage is minor, it may be possible to repair or replace the damaged parts. However, significant damage may necessitate replacing the gauge entirely.
3. Pressure Leaks: Air compressor gauges can develop leaks at the connection point or around the threads. This can result in inaccurate readings or the gauge failing to hold pressure. To address this issue, inspect the connections and tighten them securely. If there are still leaks, apply thread sealant tape or use a compatible thread sealant compound to create a tight seal. In some cases, replacing the gauge or the faulty components may be necessary.
4. Condensation or Moisture Buildup: Moisture can accumulate inside the gauge, affecting its accuracy and potentially causing corrosion. To mitigate this, ensure proper ventilation in the compressor area, use moisture traps or separators in the air compressor system, and perform regular maintenance to remove any accumulated moisture.
5. Stuck Needle or Display: Sometimes, the gauge needle or digital display may become stuck or unresponsive, preventing it from providing accurate readings. Try gently tapping or nudging the gauge to see if the needle or display responds. If the problem persists, the gauge may require repair or replacement.
Having regular maintenance, proper calibration, and addressing issues promptly are key to resolving problems with air compressor gauges. If the problems persist or if there are safety concerns, reach out to AAV and one of our qualified professionals will be more than happy to help you!